Introduction
Diesel generators play a crucial role in providing backup power during electricity outages or in remote locations where access to the grid is limited. These generators are essential for ensuring continuous operation of critical infrastructure, such as hospitals, data centers, and industrial facilities. However, like any other mechanical equipment, diesel generators are prone to wear and tear over time, which can lead to unexpected failures and costly downtime. To mitigate these risks, predictive maintenance strategies have emerged as an effective way to monitor the health of diesel generators and anticipate potential issues before they result in breakdowns. This article explores the importance of predictive maintenance for diesel generators, the key components of a predictive maintenance program, and the benefits it offers in terms of reliability, efficiency, and cost savings.
Importance of Predictive Maintenance for Diesel Generators
Predictive maintenance is a proactive approach to equipment maintenance that involves monitoring the condition of critical components and using data analysis techniques to predict when maintenance should be performed. For diesel generators, which are often relied upon for mission-critical applications, predictive maintenance can help prevent unexpected failures, reduce downtime, and extend the lifespan of the equipment. By implementing a predictive maintenance program, operators can move away from reactive maintenance practices, where repairs are only made after a breakdown has occurred, to a more strategic and cost-effective maintenance approach.
Key Components of a Predictive Maintenance Program for Diesel Generators
A successful predictive maintenance program for diesel generators typically includes the following key components:
1. Condition Monitoring: Condition monitoring involves the continuous monitoring of key parameters, such as vibration levels, temperature, oil quality, and fuel consumption, to assess the health of the generator. Advanced sensors and monitoring systems can provide real-time data on the performance of the generator and detect any anomalies that may indicate potential issues.
2. Data Analysis: The data collected from condition monitoring sensors is analyzed using advanced analytics techniques, such as machine learning algorithms and predictive modeling, to identify patterns, trends, and early indicators of equipment degradation or failure. By leveraging data analytics, operators can make informed decisions about when to schedule maintenance activities and optimize the performance of the diesel generator.
3. Predictive Maintenance Software: Predictive maintenance software platforms help streamline the data collection, analysis, and reporting process, making it easier for operators to manage and track the health of their diesel generators. These software solutions often include features such as predictive maintenance scheduling, asset health dashboards, and automated alerts for critical issues.
4. Maintenance Planning and Execution: Based on the insights gathered from condition monitoring and data analysis, maintenance activities can be planned and executed in a timely manner to address any potential issues before they escalate. This proactive approach helps minimize downtime, reduce repair costs, and maximize the reliability of the diesel generator.
Benefits of Predictive Maintenance for Diesel Generators
Implementing a predictive maintenance program for diesel generators offers a wide range of benefits for operators and facility managers:
1. Increased Reliability: By proactively monitoring the condition of critical components and addressing potential issues before they lead to failures, predictive maintenance helps improve the reliability of diesel generators. This increased reliability ensures that backup power is available when needed, minimizing the risk of disruptions to operations.
2. Enhanced Efficiency: Predictive maintenance allows operators to optimize the performance of diesel generators by identifying opportunities for efficiency improvements, such as tuning engine settings, optimizing fuel consumption, and reducing wear and tear on components. https://www.lkpowerplant.com/400kw/ leads to lower operating costs and improved overall efficiency of the equipment.
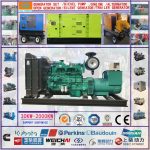
3. Cost Savings: By preventing unexpected breakdowns and minimizing downtime, predictive maintenance helps reduce repair costs, emergency service calls, and the need for costly replacement parts. Additionally, the extended lifespan of the diesel generator resulting from proactive maintenance practices translates into long-term cost savings for the organization.
4. Improved Safety: Ensuring the reliable operation of diesel generators through predictive maintenance is essential for maintaining a safe working environment, especially in critical facilities where power outages can pose significant risks to personnel and equipment. By proactively managing the health of the generator, operators can mitigate safety hazards and comply with regulatory requirements.
5. Data-Driven Decision Making: Predictive maintenance relies on data-driven insights to guide maintenance activities and optimize the performance of diesel generators. By leveraging the power of data analytics, operators can make informed decisions about maintenance priorities, resource allocation, and equipment upgrades, leading to more effective maintenance strategies and better overall outcomes.
Case Studies and Success Stories
Several organizations across various industries have successfully implemented predictive maintenance programs for their diesel generators, resulting in improved reliability, efficiency, and cost savings. For example, a large data center operator in the telecommunications industry implemented a predictive maintenance solution for its backup diesel generators, which allowed them to detect a failing fuel pump before it caused a major outage. By replacing the pump during a scheduled maintenance window, the company avoided costly downtime and maintained uninterrupted service for its customers.
In another case, a manufacturing plant implemented a predictive maintenance program for its diesel generators, which helped them identify a worn-out piston ring that was causing excessive oil consumption. By proactively replacing the piston ring, the plant was able to reduce fuel costs and extend the lifespan of the generator, leading to significant cost savings over time.
Conclusion
Predictive maintenance is a powerful tool for enhancing the performance and reliability of diesel generators in critical applications. By implementing a comprehensive predictive maintenance program that includes condition monitoring, data analysis, predictive maintenance software, and proactive maintenance planning, operators can minimize downtime, reduce repair costs, and optimize the efficiency of their diesel generators. The benefits of predictive maintenance extend beyond cost savings to include increased reliability, enhanced safety, and data-driven decision making. As organizations continue to prioritize operational efficiency and risk mitigation, predictive maintenance for diesel generators will play an increasingly important role in ensuring the availability of backup power when it is needed most.